Hydrogen Electrolysers
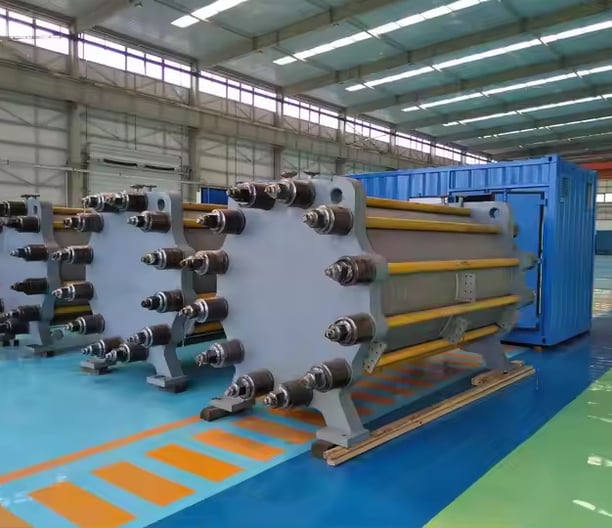
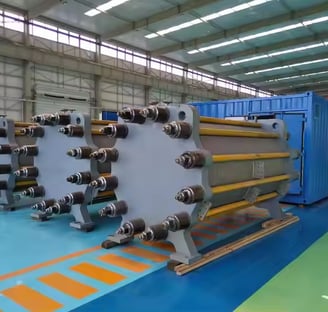
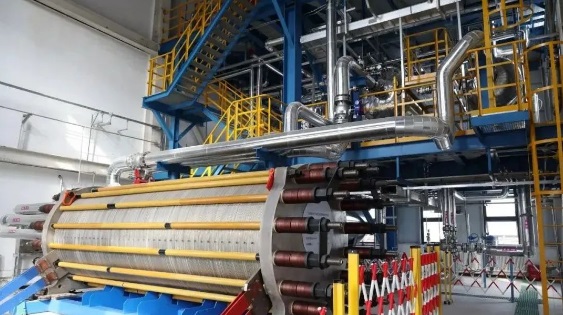

Hydrogen alkaline water electrolysis
The alkaline water electrolysis hydrogen production electrolyzer is composed of plates, diaphragms, electrodes, gaskets, pole frames, end pressure plates, screws, disc springs and insulating tubes. When direct current passes through the electrolyzer, an oxidation reaction occurs at the interface between the anode and the solution, and a reduction reaction occurs at the interface between the cathode and the solution to produce hydrogen. Optimizing the design of the electrolyzer structure and rationally selecting electrode and diaphragm materials are the keys to improving current efficiency , reducing cell voltage and saving energy consumption.
At present, the hydrogen production electrolyzer is generally a bipolar filter press electrolyzer, generally use a wiring method of "positive in the middle and negative on both sides" or "positive at one end and negative at the other end". Under the action of an external electric field, one side is positively charged and the other side is negatively charged, serving as the anode and cathode plates respectively. In other words, the same plate will have different charges on both sides, which is why it is called "bipolar". An electrolyzer with a hydrogen production capacity of 1000Nm³/h is generally composed of about 300 small chambers.
In the small chamber of the alkaline electrolyzer, the plates are located on both sides of the nickel mesh. Their role is somewhat similar to that of the electrode clamps in the laboratory. Their role is to conduct electrons, making the electrolysis current density on the plates more uniform, while reducing the contact resistance between the plates and the nickel mesh, increasing the current density, and reducing the energy consumption of hydrogen production. the plates are located at both ends of a complete small chamber structure, forming chambers for the flow of alkali solution in the cathode and anode regions.
The electrode plate consists of two parts: the main electrode plate and the electrode frame. . A complete electrode plate is obtained by welding the main electrode plate and then nickel-plating the entire plate.
Main plate
The surface of the main electrode plate inside the electrolytic chamber of the filter press electrolyzer is covered with spherical concave-convex structures (mipapillary plates). On the one hand, these concave-convex structures enable the electrode plates on both sides of the diaphragm to form reliable multi-point electrical contact in the form of "top to top". As much electrical contact as possible can reduce the contact resistance of the components inside the chamber.
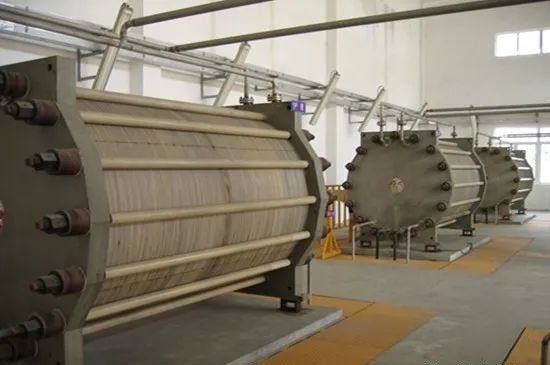
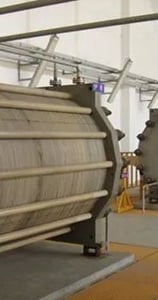
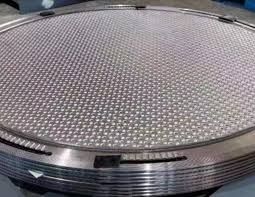
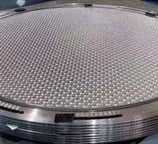
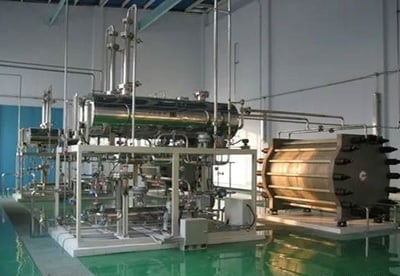
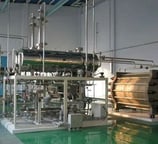
a key component in the alkaline electrolyzer, is PPS (polyphenylene sulfide) diaphragm
Serves to separate the cathode and anode and prevent the mixing of hydrogen and oxygen. At the same time, it has high ionic conductivity, which facilitates the transfer of hydroxide ions from the cathode to the anode during the electrolysis process, thereby improving the electrolysis efficiency. In addition, the PPS diaphragm has excellent high temperature resistance, chemical stability and mechanical strength, and can adapt to the harsh environment
Production process of PPS diaphragm mainly includes raw material processing, spinning and weaving, shaping and modification, and performance testing.
PPS is an acid- and alkali-resistant polymer resin with no hydrophilicity. Hydrophilicity So in order to make the PPS diaphragm have a certain degree of hydrophilicity, it must be modified.
Modification method of PPS diaphragm is as follows:
several types of processing before weaving:
1. pre-treat pure PPS fibers by immersing them in a sodium hyaluronate solution containing dilute nitric acid for 2-4 hours; after taking them out, they are then washed with deionized water and dried .
2. Mix polyphenylene sulfide and zirconium oxide nanoparticles, melt blend and extrude granulation, melt spin to obtain modified PPS fibers, then weave the fibers into yarns, and weave them into fabrics through a loom.
Treatment after weaving into cloth:
1. Sulfur fumigation to treat PPS diaphragms. This is because the molecular structure of PPS diaphragms contains benzene rings and sulfide bonds. During sulfur fumigation, sulfur may interact with certain active sites in PPS, introduce new chemical groups or change the molecular structure to improve the hydrophilicity of the diaphragm.
2. Wash and dry the PPS woven diaphragm cloth in deionized water and ethanol successively; then soak it in a halogenated alkane solvent, take it out and dry it; then soak it in a good organic solvent of polyphenylene sulfide under ultrasonic conditions; then carry out a sulfonation reaction (the sulfonation reagent includes at least one of concentrated sulfuric acid, fuming sulfuric acid, chlorosulfonic acid, and sulfur trioxide), then wash and dry it to obtain a hydrophilically modified PPS alkaline electrolytic water diaphragm.
3. Modified solutions (MOFs, in order to protect the rights and interests of the right holders, the formula will no longer be announced). The diaphragm cloth is soaked in the modified solution and then dried, and then hot-pressed. The hot-pressed diaphragm is placed in deionized water and rapidly cooled to obtain a hydrophilic PPS diaphragm.
4. Place the polyphenylene sulfide fabric diaphragm in a chlorosulfonic acid solution for chlorosulfonation, then place it in an ethylenediamine solution for amination, then place it in a glutaraldehyde solution for treatment, and then place it in a chitosan solution for reaction to obtain a hydrophilic PPS diaphragm.
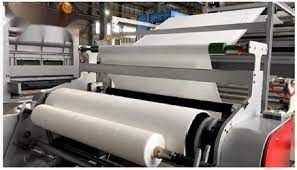
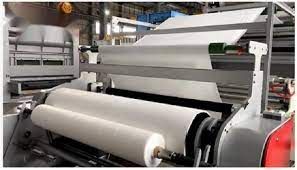
Top rated by 100+ clients
★★★★★
Predict the future by creating efficient Hydrogen Electrolysis
The hydrogen production electrode is an important component of the electrolyzer. Its manufacturing process generally includes four processes: nickel ingot drawing - nickel wire weaving into mesh - nickel mesh thermal spraying - activation (optional, there is an activation-free version).
Electrode manufacturers usually buy nickel mesh, and then spray and activate it to get the electrode. There are also nickel wire + mesh + activation.
The detailed process steps are as follows:
1. Nickel ingot drawing
The preparation process of pure nickel wire generally includes smelting, wire drawing and annealing. First, the high-purity nickel material is smelted, and a high-purity nickel billet can be obtained through the smelting process. Then, the nickel billet is drawn through a wire drawing machine and gradually becomes thinner into the required wire shape. Finally, through annealing treatment, the pure nickel wire has better mechanical and electrical properties.
The electrode mesh weaving process uses pure nickel wire of grade N6 in accordance with GB/T 5235, and the nickel content should be guaranteed to be >99.5 wt%. The commonly used wire diameters of metal wire braiding mesh can be 0.19 mm and 0.25 mm. The maximum allowable deviation of the wire diameter before braiding the metal wire braiding mesh should comply with the +0.025 mm/-0.006 mm specified in 4.2.1 of JB/T 7860.
The processing cost of nickel ingot wire drawing is also relatively transparent, generally nickel ore price + 15-20 usd/ton. There are many domestic companies doing this.
2. Nickel wire woven into a mesh
The mesh number of the metal wire mesh for alkaline water electrolysis electrode is 40 mesh, 46 mesh or 60 mesh. The thickness of the 46 mesh metal wire mesh with a wire diameter of 0.25 mm is 0.52 mm-0.60 mm; the thickness of the 40 mesh metal wire mesh with a wire diameter of 0.19 mm is 0.35 mm-0.40 mm. The specific gravity of the 46 mesh metal wire mesh with a wire diameter of 0.25 mm is 0.72 kg/m2-0.80 kg/m2; the specific gravity of the 40 mesh metal wire mesh with a wire diameter of 0.19 mm should be greater than 1.52 kg/m2.
Visually inspect the defects of the metal wire mesh. There should be no foreign matter such as oil film on the surface of the metal wire mesh, and there should be no defects of the following types: broken wires, holes, cracks, half-cut wefts, sparse and dense paths, skipped wires, loose wefts, loose warps, and sparse warps. The appearance inspection should be a full inspection.
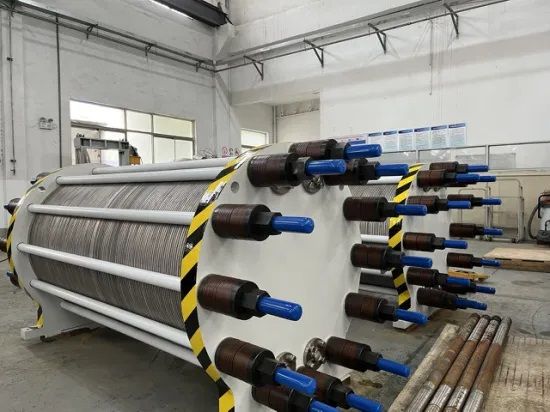
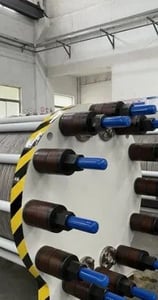
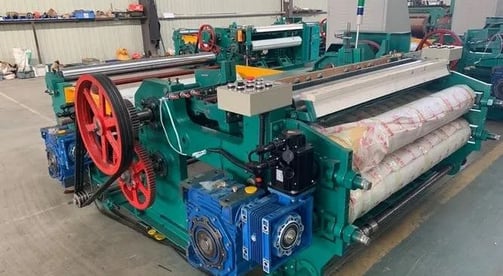
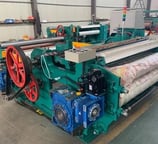
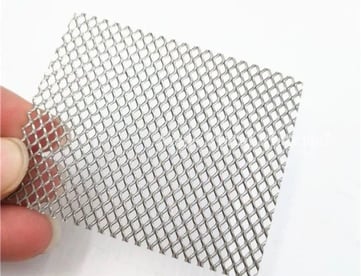
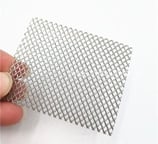
Services
Expert consultancy in hydrogen , CCUS and ASU technical solutions.
Solutions
Innovation
© 2024. All rights reserved.