Innovative Energy Solutions
Expert consultancy in green and blue hydrogen, CCS, and air separation technologies for your business needs.
Air Separation Plants Industry and Solutions
Air separation is already a mature field. What exactly is air separation? Equipment that separates air to produce oxygen, nitrogen, argon and other gases is collectively called air separation. What are the specific methods of air separation? And what is the use of each air separation equipment?
1) What are the methods of air separation ?
1) Deep freezing method: First, liquefy the air, and then use the difference in boiling points of oxygen and nitrogen to separate oxygen and nitrogen through distillation process in a certain equipment (distillation tower). This method is the most economical in large air separation units. It can also produce oxygen and nitrogen products with very high purity. As shown in the figure:
Small air separation equipment Category: Air separation engineering and air separation complete equipment
The medium pressure and full low pressure process are adopted to produce products with high purity, stable performance and large gas output. The introduction of low pressure process into small air separation greatly reduces the energy consumption of products and the investment of users. The main specifications are: 150, 180, 300, 350, 600,800m3/h,1000m3/h and other series of products. It can be designed according to user requirements.
The instrument control methods include machine room cabinet, central control room and computer control for users to choose.
Product name: Large and medium-sized air separation equipment Category: Air separation engineering and air separation complete equipment
The low-temperature process of molecular sieve purification, pressurization and expansion, structured packing on the tower, and full distillation to produce argon is adopted. The main products are 1000, 1500, 3200, 4500, 6000, 6500, 10000, 15000, 20000, 23500, 28000,30000m3/h、40000m3/h grade series air separation equipment.
It can be designed according to the specific conditions and requirements of users to meet the special requirements of different uses.
It can also produce oxygen and nitrogen gas and liquid products (including low-purity equipment and high-purity equipment) as well as all or part of argon, neon, krypton and xenon gases according to user needs.
Since 1958, world has successfully trial-produced the first3350m3/h air separation equipment, large and medium-sized air separation processes have gone through aluminum belt regenerator freezing high and low pressure air separation process, stone regenerator freezing full low pressure air separation process, switchable heat exchanger freezing full low pressure air separation process, normal temperature molecular sieve purification full low pressure air separation process, normal temperature molecular sieve purification boost expansion air separation process, normal temperature molecular sieve purification packing type upper tower full distillation argon production process. Brief introduction of each process is as follows:
1. Aluminum belt regenerator freezing high and low pressure air separation process ( referred to as the first generation of air separation )
Aluminum belt regenerator freezing high and low pressure air separation process is the leading process of China's earliest large and medium-sized air separation equipment, marking that China's manufacturing of air separation equipment has achieved a leap from small to large.
Typical products:3350m3/h(20℃State) air separation equipment, which is the first generation of air separation products in China. The process organization is relatively complex, mainly composed of air filtration and compression, high-pressure air compression, CO2 alkali washing, ammonia precooling, expansion refrigeration, heat exchange, distillation and other systems.
[Process characteristics]
(1) The processing air pressure is divided into two levels: low pressure (0.53~0.57MPa) and high pressure (16~20MPa). The cooling capacity of the air separation equipment comes from three aspects: the coke soup effect of air at two pressure levels, nitrogen expansion refrigeration and ammonia precooling system refrigeration.
(2) Two oxygen and nitrogen regenerators are used (one for positive flow and the other for reflux), filled with coiled aluminum strip fillers for heat exchange and removal of moisture and CO2 in low-pressure air. The self-cleaning effect of the regenerator is ensured by the reflux gas volume being greater than the positive flow gas volume. Usually, the ratio of the reflux to positive flow gas flow is 1.03~1.04 times.
(3) A pair of high-pressure heat exchangers are used to cool the high-pressure air. The CO2 in the high-pressure air is washed by the alkali solution of the alkali washing tower, and the water is removed by freezing the ammonia precooling system.
(4) The condenser evaporator is divided into two parts: the main cooling part and the auxiliary cooling part. The auxiliary condenser evaporator is placed lower than the main condenser evaporator. The liquid oxygen level difference is used to make the liquid oxygen in the upper tower continuously flow into the auxiliary condenser evaporator. At the same time, the pressure nitrogen introduced from the top of the lower tower
is gasified into oxygen, and then introduced into the acetylene separator to absorb acetylene and output as part of the product oxygen, which ensures the safe operation of the distillation tower. The main condenser evaporator is a shell and tube type (a total of 17749 shells and tubes, temperature difference 1.8K), and the auxiliary condenser evaporator is a coil type (temperature difference 3.2K).
[Process Disadvantages]
(1) The process organization is relatively complex. In order to provide part of the cooling capacity required by the air separation equipment and to solve the problem of removing moisture and CO2 in the high-pressure air caused by this, a number of units such as a high-pressure air compressor, an alkali scrubber, and an ammonia precooling system were added outside the cold box. At the same time, there were many devices inside the cold box, which made the operation and maintenance of the entire air separation equipment inconvenient.
(2) The self-cleaning problem of the regenerator has not been properly solved. Although the mass transfer and heat transfer of oxygen (or nitrogen) and air are staggered at different time intervals, they are carried out in the same cavity, which greatly pollutes the purity of the product. The purity of oxygen has dropped from 99.5% O2 to 99% O2, and the purity of nitrogen has dropped from 99.8% N2 to 98% N2. The latter can only be vented due to its lower purity. In addition, the temperature difference at the hot end of the regenerator is large (5℃), insufficient reheating loss is large.
(3) The expander structure is an impulse fixed nozzle type, with low efficiency, only about 60%. If air is used as the expansion medium, how to deal with the expanded air has not been properly solved, affecting the organizational level of the air separation process.
(4) The oxygen extraction rate is low, generally only 83.3%.
(5) The energy consumption is high, the design value is 0.66kWh/m3O2, while the actual operating value is as high as 0.7~0.9kWh/m3O2.
2. Stone condenser freezes the full low-pressure air separation process ( referred to as the second-generation air separation ) Tubular stone condenser freezes the full low-pressure air separation process, which is the second-generation air separation product in China. It is mainly composed of air filtration and compression, air precooling, expansion refrigeration, heat exchange, distillation and other systems. Typical products:
6000 m3/h air separation equipment, marking that China's gas separation and liquefaction equipment industry has officially entered the era of all-low-pressure air separation process.
[Process characteristics]
(1) Adopting a reaction fixed nozzle turbine expander. The air is expanded twice in the fixed nozzle and impeller, which greatly improves the efficiency of the expander (up to 80%), and the refrigeration means of the air separation equipment has been improved, so it is possible to transform the processing air from the two pressure levels of the first generation of air separation process to a pressure level of only 0.5MPa (G), realizing the transformation of high-low pressure air separation process to all-low pressure air separation process.
(2) The aluminum belt regenerator is replaced by a stone regenerator, so that the product oxygen and nitrogen always go through the internal heat exchange of the coil, ensuring that the purity of oxygen and nitrogen is not polluted, so that the purity of oxygen reaches 99.6% O2 and the purity of nitrogen reaches 100×10-6 O2.
(3) In order to remove the CO2 and moisture frozen on the stone, in addition to the method of alternating the positive flow air and the reflux polluted nitrogen, the intermediate extraction method is also adopted, that is, the air equivalent to 10% of the processed air volume is extracted in the middle of the cold storage device, which ensures that the positive flow volume below the extraction port is less than the self-cleaning requirement of the reflux volume, further reducing the temperature difference at the cold end of the cold storage device, making the self-cleaning more thorough.
(4) The expanded air is sent to the middle of the upper tower to participate in distillation, making full use of the distillation potential of the upper tower and improving the oxygen extraction rate (up to 84%).
(5) The forced circulation composed of a circulating liquid oxygen pump and a liquid oxygen adsorber is used to remove hydrocarbons such as acetylene in the liquid oxygen, ensuring the safe operation of the air separation equipment and eliminating the auxiliary condenser evaporator of the previous process.
(6) The energy consumption has been significantly reduced compared with the first generation of air separation, reaching 0.55~0.6kWh/m3O2.
【Process Disadvantages】
(1) The specific surface area per unit volume of the stone filler in the tubular stone cold storage tank is only 1/5 of that of the aluminum strip, but its density is much greater than that of the aluminum strip. Therefore, to handle the same amount of air, the stone cold storage tank is more than 5 times larger than the aluminum strip cold storage tank, which makes the stone cold storage tank bulky and heavy. The required installation foundation must be deep and solid, occupying a large area and costing a lot of money.
(2) Since the intermediate air extraction method is used to ensure the non-freezing property of the cold storage tank, the corresponding air extraction valve box and CO2 adsorber are set up, which complicates the equipment and piping in the cold box.
(3) The expander adopts a fixed nozzle and can only adjust the gas volume by adjusting the pressure. Therefore, the expansion volume adjustment range is small, and the adaptability to the variable working conditions of air separation production that requires a large amount of cold capacity is poor. The only way to solve the problem of cold capacity adjustment is to use an expansion machine to increase the equipment, which is very uneconomical.
(4) The main condenser evaporator is still a long tube type, with a large number of tubes, large volume and difficult manufacturing.
3. Switching heat exchanger freezing full low-pressure air separation process ( referred to as the third generation air separation ) With the successful development of high-efficiency plate-fin heat exchangers and the further development of reaction turbine expander technology, the level of air separation process has been greatly advanced, and the switching heat exchanger freezing full low-pressure air separation process has appeared, which is the third generation of air separation products in China. It is mainly composed of air filtration and compression, air precooling, expansion refrigeration, heat exchange, distillation (including argon extraction equipment) and other systems. Typical products:
10000m3/h air separation equipment
[Process characteristics]
(1) The plate-fin heat exchanger replaces the stone cold storage device, shell-and-tube condenser evaporator, coil-type supercooler, liquefier, etc., which greatly reduces the size of the unit equipment, and the cold box of the air separation equipment is also reduced accordingly, the cooling loss is reduced, the expansion volume is reduced, the start-up time is shortened, and a series of virtuous cycles improve the technical and economic efficiency of the air separation equipment.
(2) After the stone cold storage device is replaced by the switching heat exchanger, the intermittent heat exchange of the cold storage device is replaced by the partition wall continuous heat exchange, which makes the temperature field distribution more stable. At the same time, the space for water and CO2 freezing in the air flow channel is also increased, so that the switching cycle can be extended, and the switching loss can be reduced from 4% of the cold storage device process to 2%.
(3) The circulation method is used to ensure the non-freezing property of the switching heat exchanger, which can make the temperature difference between the cold end of the air and the return nitrogen gas from the cold storage device process.3.5℃Zoom out to2.5℃This is a relatively complete non-freezing method. It no longer requires additional equipment such as the intermediate exhaust valve box and CO2 adsorber, which simplifies the process.
(4) The turbine expander with a reactionary adjustable nozzle makes the efficiency of the expander change smoothly and has strong adaptability to variable operating conditions. At the same time, motor braking is used to recover the external work of the expander.
(5) A switching butterfly valve with a small size, light weight and large flow capacity is used to replace the bulky forced switching valve, making the layout compact.
(6) The oxygen extraction rate is increased to ~87%.
(7) Energy consumption is greatly reduced.10000m3/h air separation equipment is generally 0.49~0.52kWh/m3O2,6000m3/h air separation equipment is generally 0.53 ~ 0.55kWh / m3O2.
[Process Disadvantages]
(1) In order to meet the self-cleaning requirements of the switchable heat exchanger, a large amount of reflux dirty nitrogen is required. Generally speaking, the ratio of dirty nitrogen to total processed air volume shall not be less than 55%, that is, the output of pure nitrogen can only reach 45% of the total processed air volume. In this way, the ratio of pure nitrogen to oxygen output can only reach 1:1 at most, which cannot meet the user's demand for a large amount of pure nitrogen.
(2) In order to meet the non-freezing requirements of the switchable heat exchanger, a minimum temperature difference must be guaranteed at the cold end. The startup of the air separation equipment must be completed in four stages to avoid moisture and CO2 from entering the distillation tower. Therefore, the startup operation must be very careful and troublesome.
This type of process is the focus of the next step of technical transformation due to its backward technology, complex operation and maintenance, and short operation cycle.
4. Normal temperature molecular sieve purification full low-pressure air separation process ( referred to as the fourth generation air separation )
With the development of molecular sieve purification technology in the world and its wide application in air separation equipment. The "front-end purification" technology outside the molecular sieve purification air cold box represents the leading direction of the development of international air separation equipment processes in the 1970s. The process equipment is mainly composed of air filtration and compression, air precooling, molecular sieve purification, expansion refrigeration, heat exchange, distillation and other systems.
Typical products:6000m3/h air separation equipment
[Process characteristics]
(1) Using the characteristics of molecular sieve adsorbents to adsorb moisture, carbon dioxide and hydrocarbons in the air at room temperature, the heat transfer and mass transfer functions of the switchable heat exchanger are separated from each other. Molecular sieve adsorbers are used outside the cold box to remove moisture and CO2 in the air, and the heat exchanger inside the cold box only plays a heat exchange role. This not only makes the air entering the cold box purer, but also extends the life of the heat exchanger. There is no need to set up automatic valve boxes, liquid air and liquid oxygen adsorber circulating liquid oxygen pumps and corresponding switching valve pipelines in the cold box, which simplifies the air separation process, reduces the equipment in the cold box, and facilitates operation and maintenance.
(2) Since the main heat exchanger has no self-cleaning requirements, the temperature difference at the cold end does not need to be strictly limited, which greatly increases the output ratio of pure nitrogen and oxygen, which can reach 2.3~2.5, which can meet the requirements of users who need a large amount of pure nitrogen.
(3) The switching cycle of the molecular sieve adsorber is 108 minutes, which is much longer than the switching cycle of the switching heat exchanger of 3.5 minutes. Therefore, the air switching loss is greatly reduced, from the usual 2% of the total processed air volume to 0.5%, which is beneficial to the improvement of oxygen extraction rate. At the same time, the reduction in the number of switching times reduces the fluctuation interference caused by the switching of the distillation tower, which is beneficial to the extraction of argon.
(4) The molecular sieve adsorber removes harmful impurities in the air more thoroughly, and the operation safety of the air separation equipment is good, and the continuous operation cycle can reach more than two years.
(5) During the startup and operation process, there is no need to consider the impact of self-cleaning, so the operation is simple, which is conducive to realizing variable load operation and improving the level of automation control.
(6) The oxygen extraction rate is increased to 90-92%, and the argon extraction rate is ~52%.
[Process Disadvantages]
In order to ensure that the molecular sieve adsorber can operate at an optimal temperature of 8~10℃In order to give full play to the adsorption effect of the molecular sieve adsorbent, a refrigeration unit is set up; at the same time, an electric heater is set up for heating and desorption of the molecular sieve adsorbent. In order to ensure that the dirty nitrogen has sufficient pressure during regeneration, the exhaust pressure of the air compressor should be appropriately increased. These lead to energy consumption that is ~4% higher than the switching heat exchanger process, about 0.51~0.57kWh/m3O2.
Although the use of room temperature molecular sieve has the advantages of less switching loss and convenient operation and maintenance, it has fatal disadvantages due to its high energy consumption and was soon replaced by the new room temperature molecular sieve purification air separation process with a booster expander.
5. Normal temperature molecular sieve purification, pressurization and expansion air separation process ( referred to as the fifth generation air separation )
In the search for ways to reduce energy consumption, the emergence of normal temperature molecular sieve purification, pressurization and expansion air separation process is a major advancement in air separation process technology. During this period, domestic air separation equipment manufacturers have applied this technology and achieved the upgrading of a full range of air separation equipment with oxygen production capacity from small to large, making the overall performance of China's air separation equipment close to the international advanced level in the 1980s.
Typical products:6000m3/h air separation equipment.
[Process characteristics]
(1) Based on the normal temperature molecular sieve purification full low-pressure air separation process, the brake generator of the expander is changed into a supercharger. The function of the supercharger is to use the work generated by the expanded air during the expansion process to directly pressurize the air entering the expander, so that the pressure before the expander increases, which increases the refrigeration capacity of the unit expanded air. Under the condition that the required cooling capacity of the air separation equipment is constant, the amount of expanded air is reduced, and the total amount of processed air is correspondingly reduced, so that the oxygen extraction rate of the normal temperature molecular sieve purification supercharged expansion air separation process is further improved and the energy consumption is further reduced. The extraction rate of the fifth generation of air separation can reach 93% to 97%, and the argon extraction rate is 54% to 60%.
(2) A three-dimensional flow impeller designed with fully controllable vortex theory and a single-shaft air turbine compressor with full isothermal cooling are adopted.
(3) A molecular sieve adsorber with a vertical single-layer bed internal insulation structure is adopted.
(4) The control and regulation requirements of the computer distributed control system for the air separation process are successfully realized, which brings the level of automation control to a new level.
(5) Since the amount of processed air is reduced by ~4%, the energy consumption is equivalent to that of the switchable heat exchanger freezing full low-pressure air separation process, which is about 0.47~0.53kWh/m3O2.
6. Normal temperature molecular sieve purification packing type upper tower full distillation argon production air separation process ( sixth generation air separation )
Normal temperature molecular sieve purification boosted expansion air separation process has been widely adopted as the leading process in the international air separation industry. However, in order to further improve the efficiency of air separation equipment and reduce energy consumption, in the early 1980s, some well-known foreign air separation manufacturers began to apply structured packing technology to air separation equipment. By the 1990s,
air separation equipment using structured packing and full distillation hydrogen-free argon production technology had been fully promoted to industrial application. It is mainly composed of air filtration and compression, high-efficiency air pre-cooling, molecular sieve double-layer bed purification, boosted expansion refrigeration, heat exchange, distillation and full distillation argon production systems.
Typical products: 6000,20000m3/h air separation equipment
[Main features]
(1) Inherits all the advantages of the fifth generation of air separation: simple process, convenient operation and maintenance, DCS distribution system, less switching loss, complete removal of hydrocarbons, good operational safety of air separation equipment, continuous operation cycle of more than two years, etc.
(2) The structured packing type upper tower is used instead of the sieve plate type upper tower. The upper tower resistance is only 1/4 to 1/6 of the corresponding sieve plate tower, which reduces the exhaust pressure of the air compressor from 0.65MPa (A) to 0.61MPa (A), saving 5% to 7% of the energy consumption of the air compressor.
(3) Due to the lower operating pressure of the upper tower and greater operating flexibility, the oxygen extraction rate of the air separation unit is further improved. The oxygen extraction rate of the distillation tower can reach 99.5%; the oxygen extraction rate of the air separation equipment is 97% to 99%.
(4) The preparation of refined argon is directly obtained by low-temperature distillation, that is, the full distillation (hydrogen-free) argon production technology is adopted in one step. It saves 3% to 4% of the energy consumption of hydrogen production. At the same time, the argon extraction rate of the distillation tower is greatly improved, which can reach 65% to 84%. The quality of the refined argon product is high: the oxygen content can be lower than 2ppmO2.
(5) It adopts a high-efficiency air precooling system. The air precooling system is equipped with a water cooling tower, which makes full use of the hygroscopicity of dry nitrogen to reduce the cooling water temperature and reduce the refrigeration load of the chiller. Depending on the user's nitrogen usage, no additional chiller is required.
(6) The molecular sieve purification air system adopts an activated alumina-molecular sieve double-layer bed structure, which greatly extends the life of the molecular sieve and reduces the bed resistance.
(7) It adopts high-efficiency booster turbine expander technology, and the expander efficiency can reach 83% to 88%.
(8) It adopts advanced DCS computer control technology to realize the integrated control of central control, machine side and on-site, which can effectively monitor the production process of the entire air separation equipment. The complete control system has the characteristics of advanced and reliable design and high performance-price ratio.
(9) The sixth-generation air separation equipment has significant energy-saving effects due to the adoption of a number of new technologies. Compared with the fifth-generation air separation equipment, the total energy consumption of the equipment has decreased by about 8% to 10%, and the energy consumption for oxygen production is 0.37 to 0.43 kWh/m3O2.
7. Room temperature molecular sieve purification large internal compression air separation process ?
Typical products: 16000, 28000, 30000,40000m3/h air separation equipment?
Mainly composed of air filtration and compression, air precooling, molecular sieve purification, air (nitrogen) circulation and pressurization system, expansion refrigeration, high-pressure heat exchange system, distillation and other systems.
[Process characteristics]
(1) Internal compression process air separation equipment is a process form that uses liquid oxygen pump to compress oxygen products based on the sixth-generation air separation equipment process. According to the different media compressed by the circulating booster, the process form can be divided into two processes: air circulation and nitrogen circulation. According to the different positions of the air entering the tower after expansion, the internal compression process can be divided into the process of expanding air into the upper tower and the process of expanding air into the lower tower. The internal compression process can also be divided into a single-pump internal compression process and a double-pump internal compression process according to the product compression situation.
(2) The determination of the pressure and flow of air (or nitrogen) for heat exchange with pressurized liquid oxygen; the organization of the high-pressure heat exchange system and the organization of distillation are the core issues of the internal compression air separation process. Therefore, unlike the conventional external compression process, the internal compression process must be continuously optimized and calculated according to the specific conditions such as the pressure, flow rate and usage characteristics of the final product, and a reasonable process organization method, optimal vaporization pressure and circulation flow rate must be selected to make the oxygen and argon extraction rate of the air separation equipment higher.
(3) The internal compression process eliminates the oxygen compressor, so there is no high-temperature gas oxygen, the fire hazard is small, and the safety is good. The main cooling extracts a large amount of liquid oxygen to ensure that the possibility of hydrocarbon accumulation is minimized. The product liquid oxygen evaporates under high pressure, greatly reducing the possibility of hydrocarbon accumulation. The specially designed liquid oxygen pump automatic start-up and operation program can effectively ensure the safe operation of the device and continuous oxygen supply.
(4) The low-temperature and high-pressure liquid oxygen pumps of the internal compression process are all imported products, and are online cold standby. If the operating pump fails, the standby pump will automatically reach the working load within 10 seconds. Therefore, the reliability of the internal compression process is relatively high.
Chemical and petrochemical users generally require very high oxygen pressure, so external compression must be oxygen permeation + piston oxygen compressor, while the internal compression process only uses one booster air compressor to replace two oxygen compressors, and its operating reliability is greatly increased.
(5) The high-pressure liquid oxygen pump is easy to operate and requires very little maintenance. If the main air compressor and the booster air compressor of the internal compression process are in the form of one-to-two steam turbines, the layout is compact and the footprint is small. However, the oxygen compressor requires sufficient safety distance, occupies a large area, and has high infrastructure costs.
(6) The unit product energy consumption of the internal compression process is closely related to the scale of the air separation equipment, the product pressure, and the amount of liquid products. Due to the large irreversible loss of internal compression and the slightly lower product extraction rate, the unit product energy consumption of the internal compression process is about 3% to 7% higher than that of the conventional external compression process (compared under the same product working conditions).
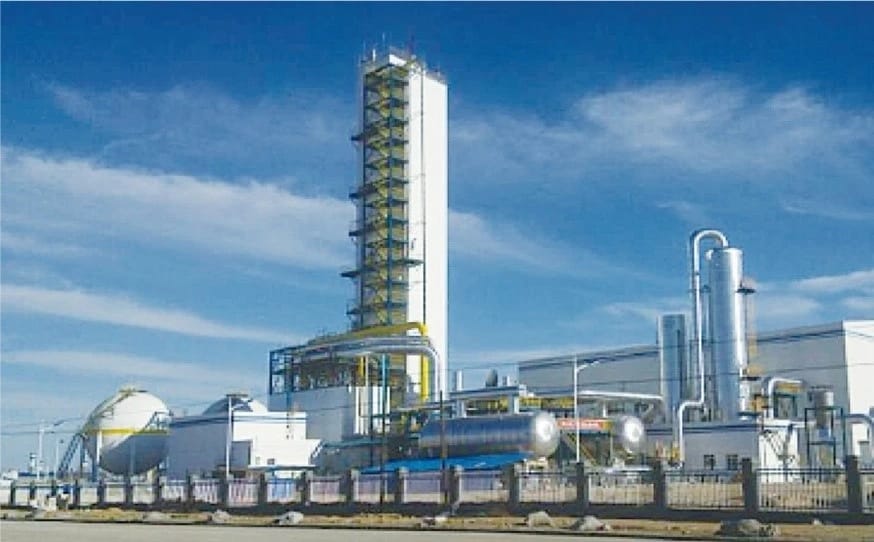
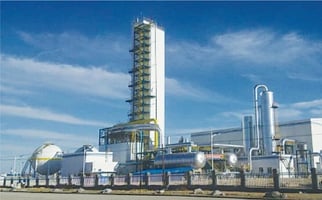
Services
Expert consultancy in hydrogen , CCUS and ASU technical solutions.
Solutions
Innovation
© 2024. All rights reserved.